
INVESTORS
BRIDGING THE GAP - A LUCRATIVE OPPORTUNITY TO MINIATURIZE INDUSTRIAL COMPONENTS
Integra Devices is addressing a very large industry need: the miniaturization in industrial components and mechanical devices (a TAM greater than $200 Billion)
Conventional micro-manufacturing leverages semiconductor-based methods to build small micro-electromechanical systems (MEMs). Using micromachining processes such as deposition, photolithography, and etching, the MEMs industry has successfully miniaturized many electro-mechanical devices, such as accelerometers, microphones, and other sensors. However, due to inherent limitations with these processes, the MEMs industry has only been able to produce a handful of products. Less than 8% of the total industrial components have been miniaturized.
Due to the large, untouched market opportunity, universities and research labs have continued to look and invest in novel ways to fabricate micro-devices. The University of California, Irvine has been a pioneer in this field, investing millions of dollars into the exploration of alternative manufacturing methods through grants from both government and industry partners.
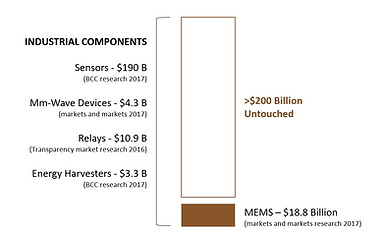
INTEGRA SOLUTION
Through 15 years of research, the University of California Irvine discovered and patented a completely new paradigm for building micro-devices. This batch-manufactured approach leverages 3D heterogeneous integration used in the microelectronic packaging industry; stacking and laminating layers instead of monolithic depositing layers. This research has demonstrated over 20 different devices that can be built using this process. This new toolbox and know-how presents a huge opportunity to develop a new breed of miniature products that could not have been built before.
Rather than develop products that compete with current MEMs solutions ($18B), Integra Devices's strategy is to miniaturize industrial components that can’t be effectively miniaturized using todays MEMs technologies ($180 B opportunity). Leveraging work already done at the university, Integra Devices is targeting high-margin, high-value products for:
-
MICROWAVE/MM-WAVE SOLUTIONS FOR 5G
-
ZERO-POWER SENSING SOLUTIONS FOR IoT

5G CHALLENGES
5G, the next generation of telecomm, aims to satisfy the connection requirements of IoT applications through the usage of mm-wave frequencies. Currently, telecom operates at roughly 2.4 GHz. 5G’s initial push is at 6 GHz, with the final bandwidths being at 28 GHz and above (mm-wave). Mm-wave frequencies can transmit larger amounts of data, however, also come with limitations:
-
Limited Range
-
Requires line of sight
-
Currently large and costly components
Due to limited range and required line of sight, higher frequencies will have smaller coverage areas per cell site, thus the mobile grid must become far denser than it is today. This is solved through the incorporation of additional macro-cells as well as small-cells, on poles, towers, rooftops, but also mass-deployment at the street level, utilizing street furniture and light poles as physical infrastructure. However, current mm-wave components make it difficult for small-cell modules to be scalable, cost-effective, and practical. Integra Device’s manufacturing technology resolves this challenge, through the batch-production of miniature, low-cost mm-wave components and substrates.
Other microwave/mm-wave markets include:
-
Aerospace & Defense
-
Test & Measurement
-
Satellite Communications

IoT CHALLENGES
The Internet of Things represents one of the largest new markets in recent tech history, promising to revolutionize the efficiency and optimization of a wide variety of industries by bringing real-world data and analytics to operations. IoT will need to connect billions of devices deployed in the physical world (the so-called “edge” of IoT) to the cloud where big data analytics can be performed.
Many, if not most, of these edge devices will require wireless operation, enabling deployment in locations where electrical infrastructure does not exist or is difficult/too costly to install. The use of wireless devices offers several advantages over existing, wired methodologies, including flexibility, ease of implementation, and the ability to facilitate the placement of sensors in previously inaccessible locations. Thus, for optimum deployability, IoT sensors need to be small, autonomous, and cost effective. Integra Device’s manufacturing technology and innovative design team enables us to build a variety of zero-power, autonomous sensor solutions.
